Over 60% of the world’s population lives in buildings made of masonry. Although such homes are convenient because of their high level of comfort and readily available building materials, their vulnerability to earthquakes raises serious concerns. To address that problem, a Japanese startup has developed a new kind of coating that, when applied to masonry, makes structures more resistant to earthquakes. The coating has already been put to practical use in Taiwan, and efforts are now underway to introduce it in the Philippines.
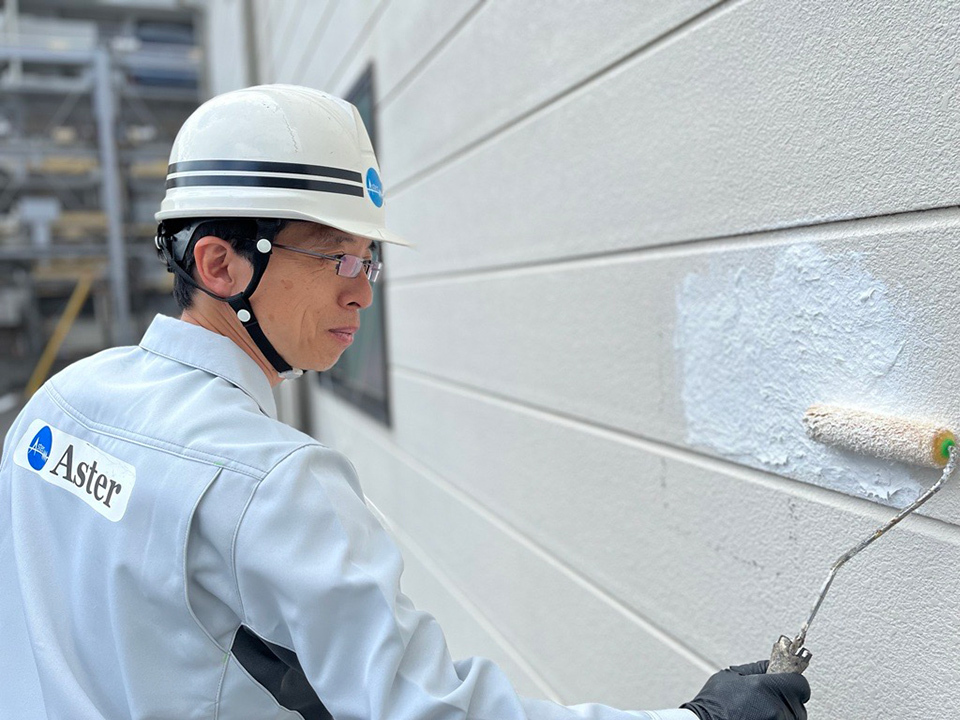
SUZUKI Masaomi, CEO of Aster Co., Ltd., applies Aster Power Coating to a wall using a roller. ASTER
Masonry, the world’s foremost method of construction, involves stacking materials such as bricks or stones. However, research by the Meguro Lab at the University of Tokyo’s Institute of Industrial Science found that 80% of fatalities caused by earthquakes over the past century were attributable to collapsing buildings, a fact that underscores the urgency of the seismic retrofitting of masonry.
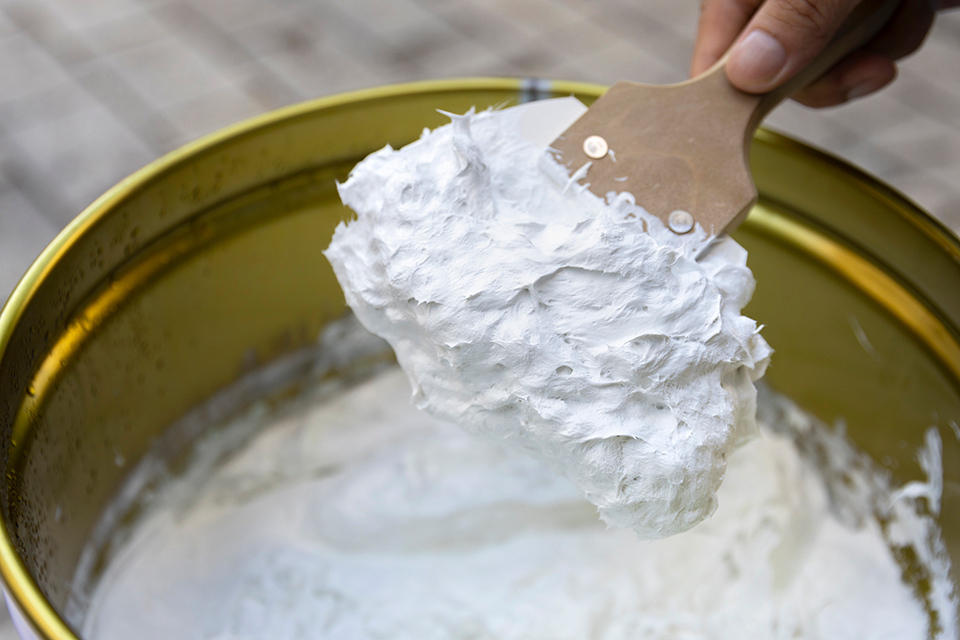
Aster Power Coating contains both glass fiber and acrylic silicone resin.
To deal with the problem, Japanese startup Aster Co., Ltd., has developed a new material, which, when simply applied as a coating on masonry surfaces, significantly improves their earthquake resistance. The material was developed by SUZUKI Masaomi and YAMAMOTO Kenjiro, now CEO and COO, respectively, of the firm.
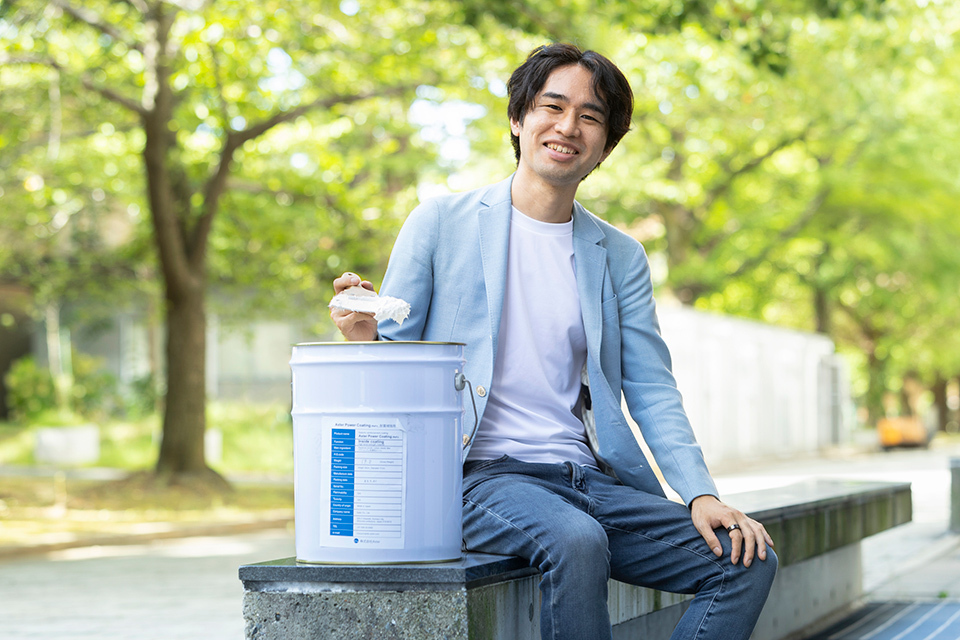
YAMAMOTO Kenjiro, COO of Aster, talks about their newly developed Aster Power Coating.
His academic advisor at the University of Tokyo, Professor MEGURO Kimiro, introduced Yamamoto to Suzuki, then CEO of SG Corporation, whose construction company specializes in using coating materials to prevent cracks in concrete. Working together, the two men developed a strong resin coating that they called Aster Power Coating. If the coating is applied to a masonry wall and left to dry for about two weeks, it becomes a strong yet flexible film—perfect, they realized, for seismic retrofitting.
The innovative product consists of short, hard glass fibers that can withstand being pulled from both ends, meaning that they won’t stretch even during tremors capable of producing small cracks in walls. In addition, the material also contains soft acrylic silicone resin, the rubber-like flexibility of which prevents walls coated with it from collapsing, even during strong tremors.
Although seismic retrofitting, which aims to improve resilience to earthquakes, normally comes at high cost—such as the installation of thicker pillars and beams, or the insertion of additional steel reinforcement—the newly developed coating has been designed to be much cheaper through its simple application to building surfaces, as it creates a rubber-like film that returns to its original shape after deformation.
Having succeeded in developing their new coating, the two men established Aster in 2019 with Shanthanu Menon as CTO, with the purpose of spreading their technology more quickly. They first set their sights on the market of the Philippines, an archipelago nation that lies in the Pacific Ring of Fire, one of the most earthquake-prone regions in the world. The country’s schools alone have 800,000 masonry-built classrooms, each in need of seismic retrofitting. With the cooperation of the Japan International Cooperation Agency (JICA), Yamamoto and Suzuki submitted a proposal to the Philippines’ Department of Public Works and Highways (DPWH) to use the new coating to seismically retrofit public schools.
Before marketing their product there, however, they brought bricks used in the Philippines to Japan to replicate local masonry conditions, then conducted controlled vibration tests on walls to compare the effects of the new coating. After subjecting the walls to simulated earthquakes with a seismic intensity of 6 out of 7 on the Japanese scale—a level of shaking at which it becomes difficult or impossible to remain standing—seven times, they found that almost no cracks had appeared in walls with the new coating applied, whereas the uncoated walls collapsed after just one test.
Watching the simulations online from the Philippines, DPWH personnel soon realized the coating’s effectiveness, and are now working on new building standards to incorporate it for use in schools throughout the country.
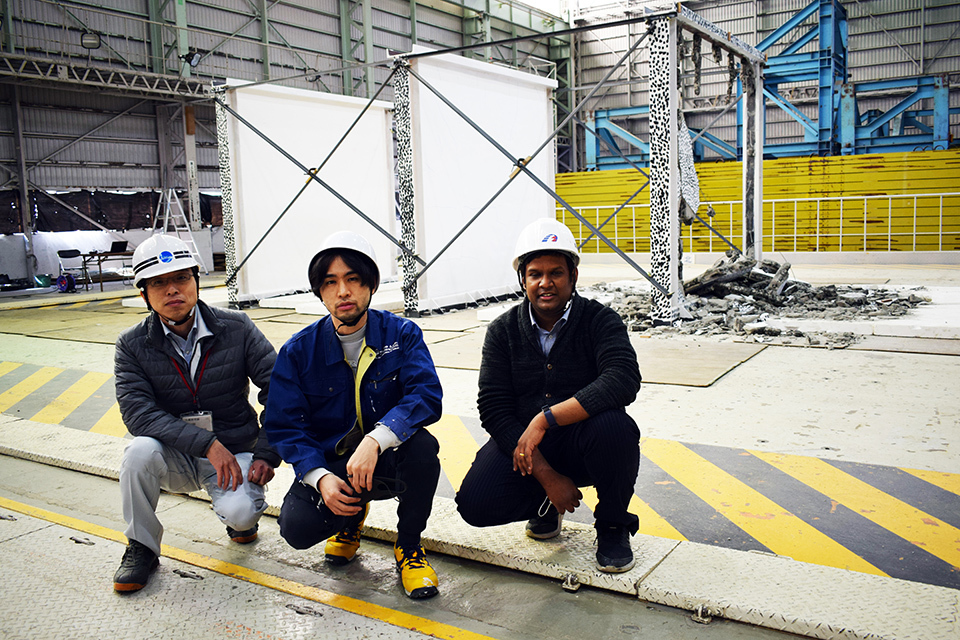
Scene from a vibration test conducted in Tsukuba City in 2022, in which walls made from blocks replicating those from the Philippines were subjected to earthquake-simulation tests. Walls without the company’s coating (background right) were destroyed, while those with an application of dried coating (background left and center) had no obvious cracks and retained their original shape. ASTER
Meanwhile, interest in the earthquake-resistant coating has also grown significantly in Taiwan, which recently suffered from a major earthquake in April 2024. After tests with local companies confirmed its effectiveness, the coating is now being applied to the walls of older buildings as well.
Yamamoto is considering ways to improve the coating as he believes it must be readily available to regular people in order to make it more widespread. Explaining why, he said, “The ideal is to be able to seismically retrofit a building without giving the task much thought. In countries where masonry construction is the norm, residents often repaint their walls themselves. I hope that our coating will be sold in stores alongside ordinary paint someday, so that consumers can buy and use it easily. As they apply more layers, the coating will thicken, gradually improving earthquake resistance without them even realizing it.”