Carbon Recycling, which recasts the role of carbon dioxide as a resource to be put to good use, has been positioned by Japan as a key technology for realizing its goal of carbon neutrality. Pioneering this new role, a domestically produced type of concrete that absorbs carbon dioxide during the curing process has already been commercialized.
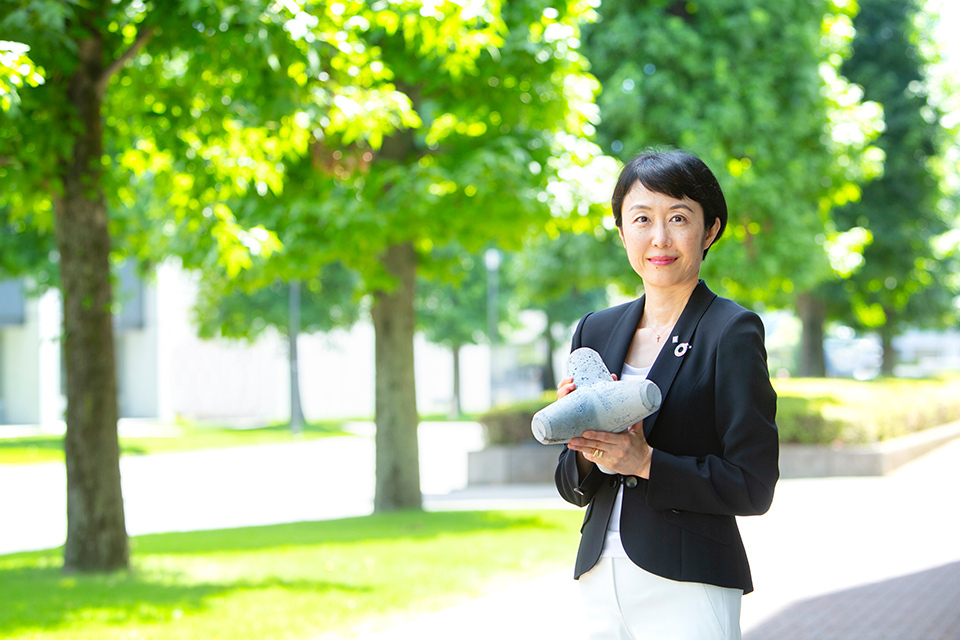
“Developing a new type of concrete takes time. We would like to keep on making products to protect people and enrich their lives by fully utilizing the accomplishments of our many years of research,” says ONO Kayoko, senior manager of the Technology Development Department of Kajima Corporation’s Civil Engineering Management Division.
The more structures that are built with it, the more that carbon dioxide emissions can be reduced from the planet—this almost magical product, a concrete called CO2-SUICOM, was created in 2008, with Kajima Corporation leading its joint development with three other companies. “The idea originated when we focused our attention on the 5,000-year-old concrete that was excavated from the Dadiwan Ruins in China, as part of our research on concrete durability,” says ONO Kayoko, senior manager of the Technology Development Department of Kajima Corporation’s Civil Engineering Management Division. The study led to the realization that carbonation, until then considered to be a cause of the corrosion of structural steel frames, was actually the key to concrete’s durability. With that serving as a hint, in 2006, Kajima developed EIEN (Earth, Infinity, ENvironment), a concrete with an estimated life span of 10,000 years. Then, the company adapted EIEN technology to give rise to CO2-SUICOM (CO2-Storage and Utilization for Infrastructure by COncrete Materials; the name was also inspired by the Japanese word suikomu, which means “absorb”), thinking that it could also reduce CO2 emissions since it absorbs CO2 during carbonation.
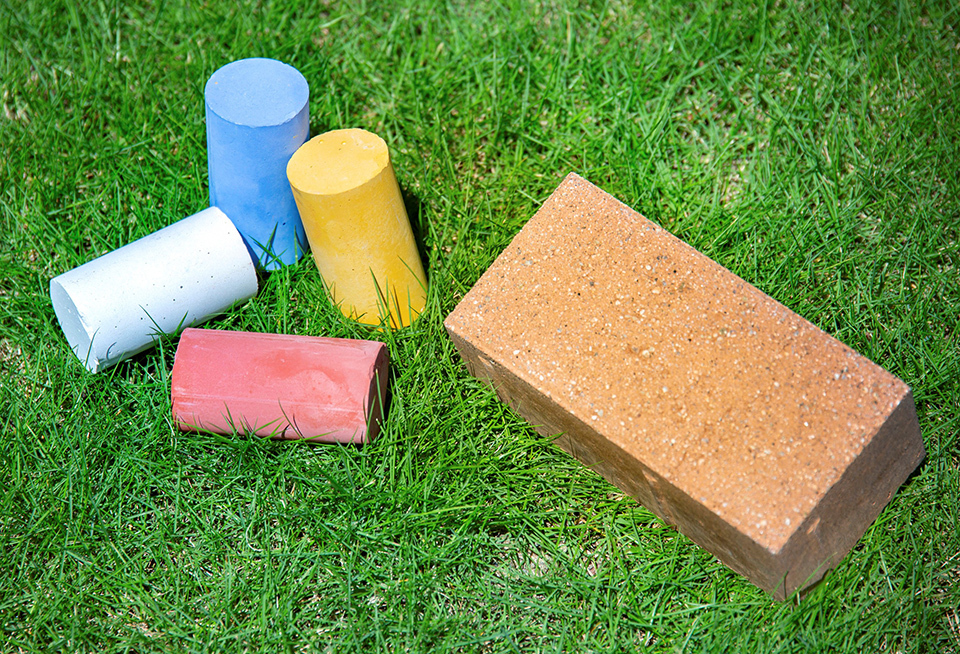
CO2-SUICOM is resistant to harsh environments because its surface becomes denser due to curing by CO2. It is also aesthetically pleasing since the carbonation process prevents efflorescence, or the appearance over time of white deposits on the surface.
Concrete is made by mixing cement—which hardens in reaction to contact with water—with aggregates such as sand and gravel. However, the cement production process emits large quantities of CO2 as it involves heating limestone to very high temperatures. In order to reduce these emissions, CO2-SUICOM uses γ-C2S, a special material that solidifies when it comes into contact with CO2. Not only does the material’s use help to cut the amount of cement needed to about one-third the usual volume, but the concrete’s net CO2 emissions fall below zero through its absorption and fixation of CO2. That process has made CO2-SUICOM the world’s first carbon-negative* concrete. While other types of CO2-absorbing concrete are available, the product’s strength lies in the amount of CO2 it absorbs: the act of producing one cubic meter of the concrete in itself absorbs more carbon than one cedar tree can in a year. “Our expertise and many years of experience have enabled us to develop the optimum mixture of ingredients and timing for CO2 absorption,” says Ono.
*a state in which reductions of CO2 exceed emissions.
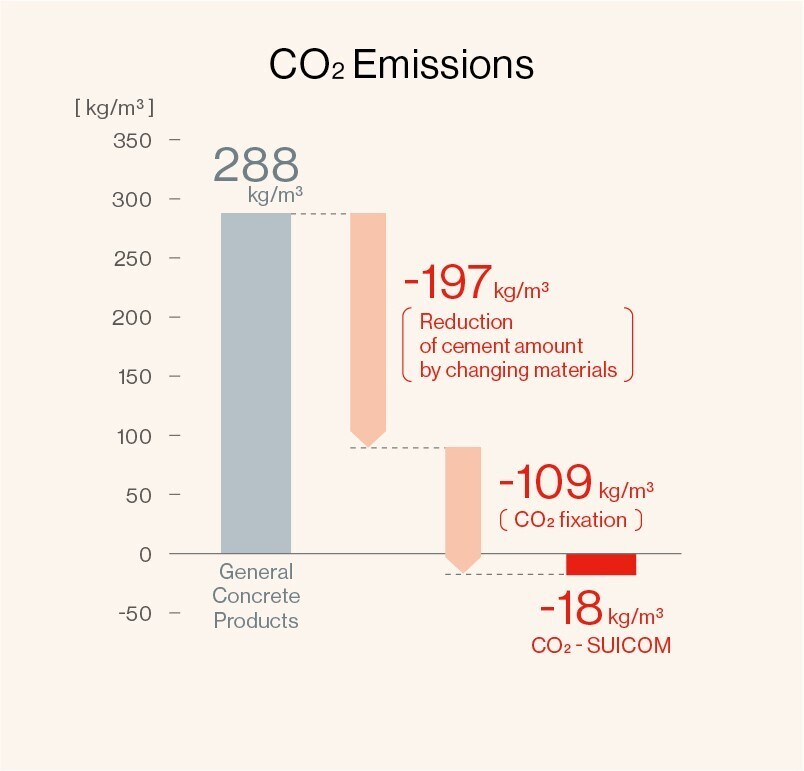
Although the concrete became commercially available in 2011, it did not enjoy widespread usage at first due to its high cost and the special equipment needed in its production that prevents casting-in-place, among other reasons. However, along with the global trend toward decarbonization, demand for the product has heightened in recent years, including inquiries from abroad. The market size for CO2-absorbing concrete is forecast to grow to between 15 and 40 trillion yen by 2030, which has led to a current acceleration in global competition to develop such a product.
The “Green Growth Strategy Through Achieving Carbon Neutrality in 2050”—the Japanese government’s industrial policy for realizing carbon neutrality by 2050—has set several ambitious goals, such as lowering the price of CO2-absorbing concrete to the same level as that of ordinary concrete by 2030, and, as part of the “Roadmap for Carbon Recycling Technologies,” the concrete’s use will be promoted in such high-demand generic products as building beams, starting from around 2040. In January 2022, as one of its projects, a consortium including Kajima Corporation was adopted by a governmental organization as the implementing body for a project based on the 2-trillion-yen Green Innovation Fund to develop concrete that maximizes the level of CO2 emissions reduction and CO2 fixation, as well as to develop related quality-control technology. For its actual social implementation, issues such as cost and on-site placement will need to be tackled.
As emerging economies grow, the global demand for concrete and cement is projected to rise by as much as 23% in 2050 over fiscal 2014 levels. That projection will have a different meaning altogether, however, if carbon-negative concrete comes into widespread use. “Concrete is an indispensable foundation of our lives. That is precisely why we want to deliver products to the world that both respond to the social issues of the time and offer high quality,” says Ono. “The first construction site that I visited when I joined the company was that of one of the largest concrete dams in Japan. I was deeply impressed by the scale of the civil engineering project and the technological skill of the experts involved, as well as by their attention to detail. I look forward to the day when such a dam is built with CO2-SUICOM.”
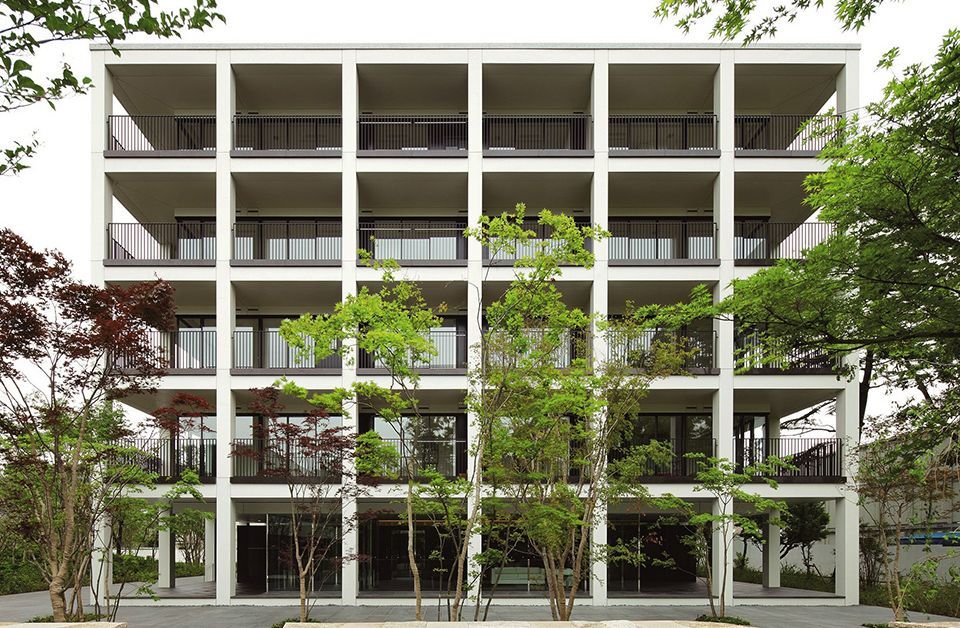
In the field of architecture, the product is used in such places as the ceilings of apartment balconies (photo). Since its dense surface prevents water intrusion, concrete skeletal structures can be effectively protected, even in areas exposed to the elements. KAJIMA CORPORATION
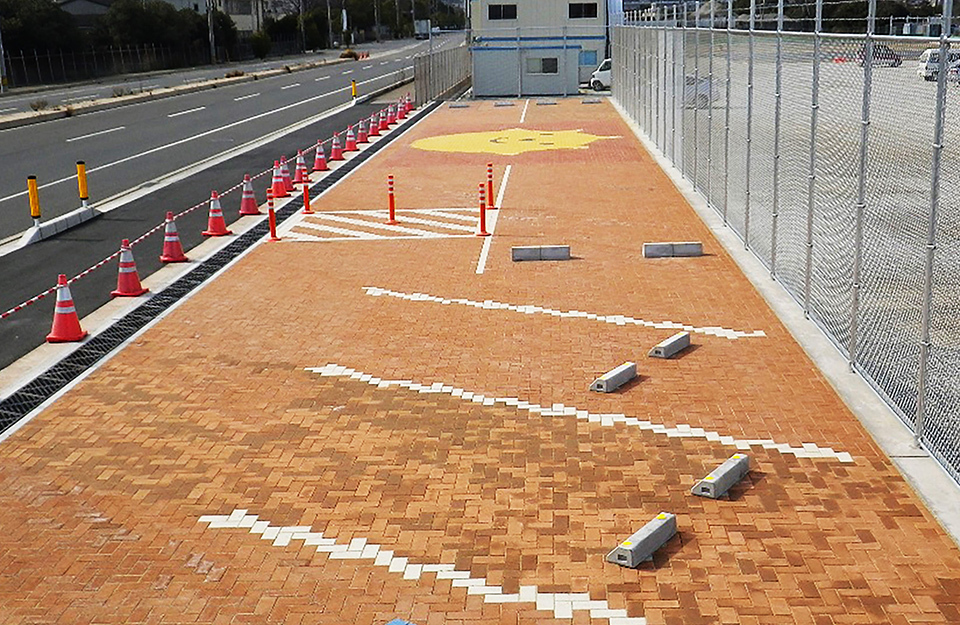
The CO2-SUICOM products are currently made at precast concrete plants with special equipment. Among the concrete’s main applications are paving blocks in parking lots (photo) and road demarcation blocks. KAJIMA CORPORATION
Left: In the field of architecture, the product is used in such places as the ceilings of apartment balconies (photo). Since its dense surface prevents water intrusion, concrete skeletal structures can be effectively protected, even in areas exposed to the elements. KAJIMA CORPORATION
Right: The CO2-SUICOM products are currently made at precast concrete plants with special equipment. Among the concrete’s main applications are paving blocks in parking lots (photo) and road demarcation blocks. KAJIMA CORPORATION