A Japanese startup is using 3D printing to develop high-quality prosthetic legs at a lower price, contributing to quality-of-life improvements for amputees living in the Philippines.
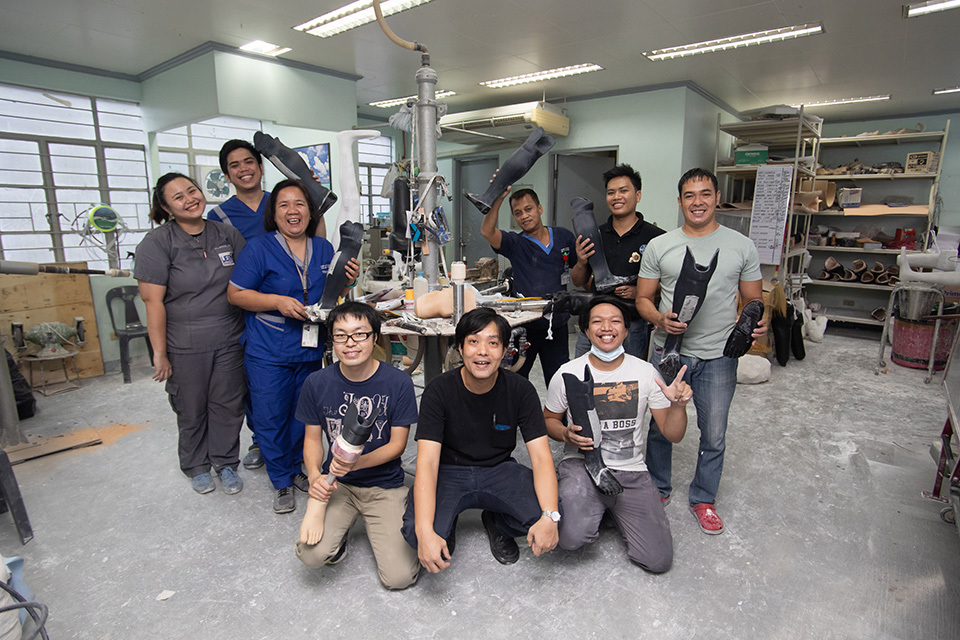
A verification test was conducted in 2018 in collaboration with the University of the Philippines General Hospital. Shown here with the hospital staff, TOKUSHIMA Yutaka, the CEO, is in the middle of the front row. On his left is prosthetist KOBAYASHI Yoshiaki.
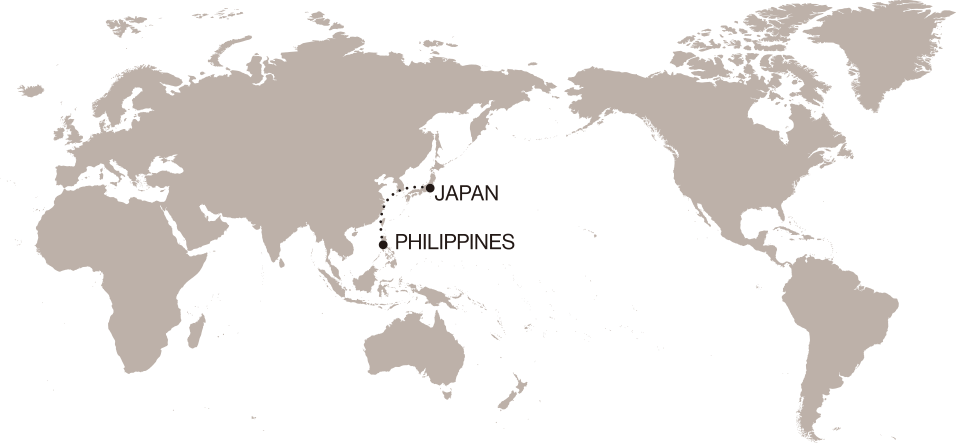
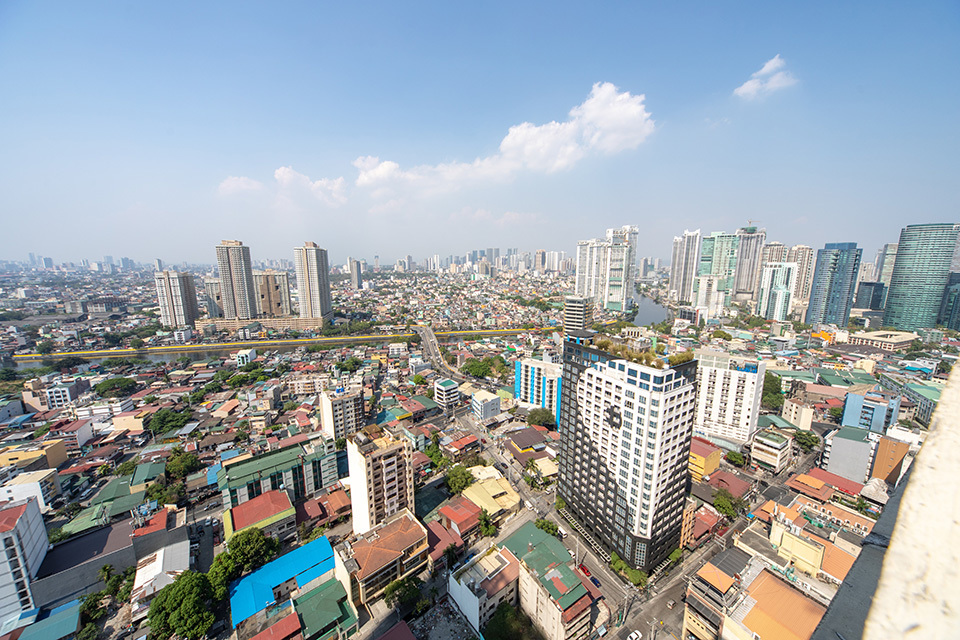
Many people in the Philippines have suffered amputations owing to such diet-related diseases as diabetes.
With Tokyo as the first city ever to host the Paralympic Games for a second time, Japan seeks to create an inclusive society and remove obstacles that prevent people from demonstrating their full potential. However, many people worldwide who have lost a leg due to illness or an accident, have had to put up with their disability as they cannot afford prostheses, which tend to be high priced. In the Philippines, for example, where diabetes is prevalent owing to a sugar-rich diet, countless poor people, unable to pay for a hospital visit, suffer from increasingly severe symptoms that force them to have a leg amputated. According to a survey commissioned in 2017 by the Japan International Cooperation Agency (JICA), there are 1.23 million people in the Philippines who need a prosthetic leg.
TOKUSHIMA Yutaka, CEO of the Japanese startup Instalimb, Inc., founded his company to give disabled people—including those in the Philippines—affordable prosthetic legs through 3D printing. After a career working for manufacturers of IT components and medical devices, Tokushima joined the Japan Overseas Cooperation Volunteers. When he visited the Philippines at that time, he noticed many people who had lost their hope along with a leg.
Because a prosthetic leg must be manually fitted, mass production is difficult. Hence, prostheses become expensive, and the poor have no choice but to go on living without one. Since many such people are manual laborers, they may lose their jobs, making them even more impoverished.
Tokushima then had an idea: “I believed that if I leveraged my knowledge, I could change the situation. I wanted to give prosthetic legs to the people who needed them.” He developed 3D design software for prosthetic legs, and in 2018, started up Instalimb basing it in Tokyo. After several attempts developing various prototypes, the company finally succeeded in designing a prosthetic leg costing only 20,000 Philippine pesos (PHP), equivalent to about USD400—the average monthly salary for a recent college graduate in the Philippines—or just one-tenth the normal price. Instalimb was also able to significantly reduce the time needed to produce prosthetic legs, which typically take more than three to four weeks to make. According to Tokushima, a 3D printer, carrying out production overnight, can perform the whole process, from measurement to completion, in as little as 24 hours.
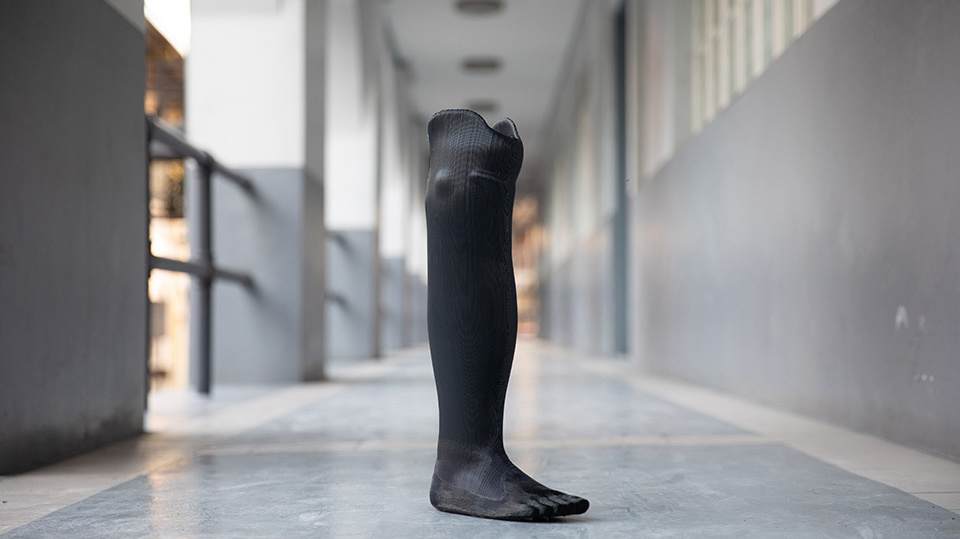
Instalimb’s prosthetic leg, made from polylactic acid carbon—a reinforced material consisting of plastic mixed with carbon—is both lightweight and comfortable to wear.
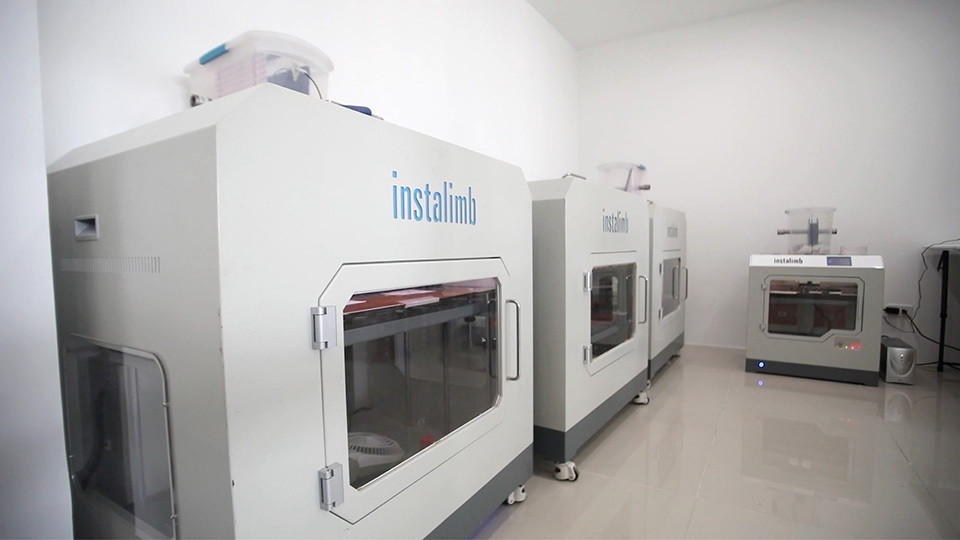
3D printers have significantly shortened the time needed to complete a prosthetic leg tailored to each person.
In 2019, Tokushima established a local subsidiary in the Philippines, where he began selling his company’s prosthetic legs. The production process begins by taking a cross-section 3D scan of the customer’s leg, based upon which Tokushima’s self-developed 3D modeling software then corrects the shape before printing. Once a preliminary mold is created, the next step is a test fitting. If any parts hurt, or any other problems arise, a prosthetist makes the necessary adjustments and applies them to the data. The finalized data is then sent to the 3D printer to create a mold.
To provide prosthetic legs to those people who need them, Tokushima thought up his simple process for creating custom-made prosthetics that are nevertheless affordable and quick to produce. Speaking about the advantages of 3D-printed prosthetic legs, KOBAYASHI Yoshiaki, the company’s prosthetist, says, “Because we can produce the item in a short time, the patient can start relearning how to walk soon after their leg is amputated, before the muscles begin to atrophy. This allows them to return to society early.”
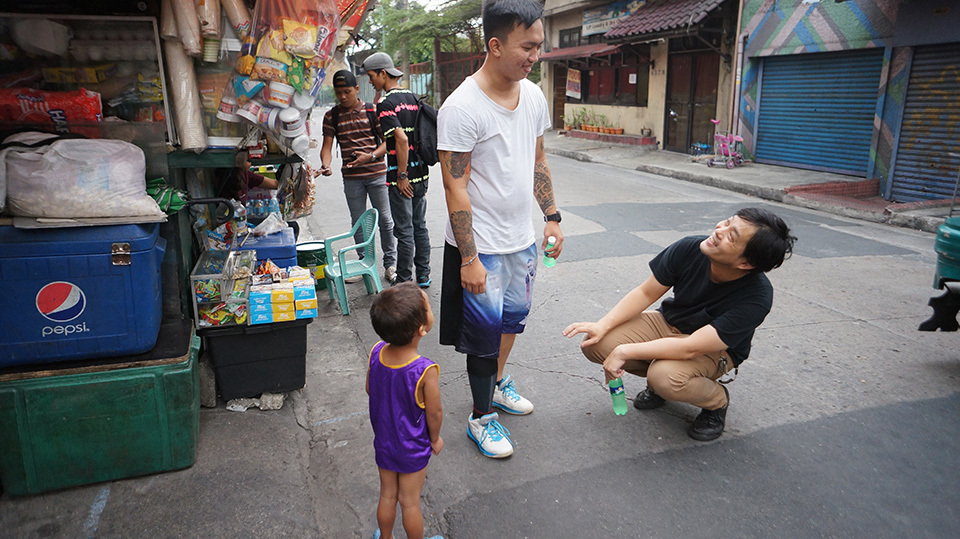
On a street in Manila, a patient who was fitted with a prosthetic leg says he has been able to return to his normal life.
Instalimb is now focusing on developing automatic designs with AI. If data on a prosthetic leg can be digitized after a prosthetist has made adjustments, the company might be able to create designs in the future even in locations where there are no prosthetists. With the COVID-19 pandemic making it difficult for people to move around and contact each other, AI offers greater promise in such cases. Henceforth, the company is considering expansion to other developing countries facing similar issues, as well as to conflict areas where many people have lost legs.
Instalimb’s policy is to “create a world where everyone in need can access prosthetics.” Tokushima says, “I hope more people will be able to newly dream of returning to their former lifestyle by obtaining a prosthetic leg and regaining their independence.”